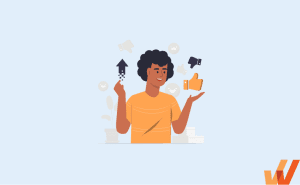
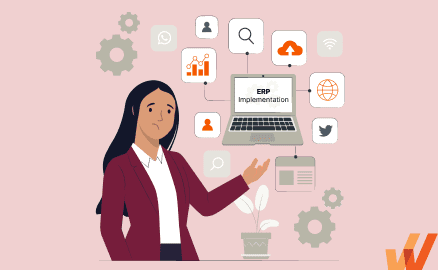
Enterprise resource planning (ERP) software implementation can be a risky proposition — it’s not unheard of for companies to mishandle the process and see their operations grind to a halt. It’s also not just big companies making a mess out of their implementations. In one study, only 67% of companies rated their ERP implementations as successful or very successful.
Not only do these failures result in negative publicity, but they can also be financially catastrophic and cause rifts in organizations that take years to mend.
Studying the causes of ERP failures to gain an understanding of what caused them to go south can help you avoid the same issues when implementing your own solution, and empower your organization to find software ROI from an ERP transformation.
8 case studies of infamous ERP implementation failures
- Hershey’s failed ERP implementation cost them over $100 million
- Mission Produce’s failed ERP transformation
- Waste Management claimed over $500 million in losses after ERP failure
- Revlon spent $50 million recovering from its ERP implementation mistakes
- Lidl lost 7 years due to a failed ERP implementation
- The US Navy wastes 7 years on ERP implementation
- Nike’s ERP implementation disaster led to $500 million in lost sales
- HP’s ERP migration caused $160 million in lost sales
How Much Can a Failed ERP Implementation Cost?
Failures in ERP implementation can reach millions of dollars. As a result of the complexity of installing new systems, development costs can quickly rise, and if there are problems with the implementation, the money is lost, and more funds need to be spent to repair the damage.
A few of the key risk areas associated with the high cost of a failed ERP implementation include:
- Setting organizations back months or years: From software development to employee training, transitioning to a new ERP takes time. A failed implementation wastes all of the hours dedicated to the project, plus the time it takes to get systems, people, and revenue back on track.
- More downtime, resulting in a loss of sales: Mistakes made during implementation lead to downtime, which can cause massive losses in current and future sales. This is especially true if an ERP is implemented to automate portions of a company’s supply chain.
- Expensive recovery costs: The initial failure of an ERP already incurs massive costs, and the fallout adds more items to the to-do list. Organizations that have experienced ERP failure are forced to shoulder additional operating costs to return to normal productivity levels.
8 Examples of ERP Implementation Failures to Learn From
According to research and statistics on ERP systems, a successful implementation can be a huge driver of innovation and productivity for organizations – with 95% of businesses saying an ERP greatly improved their business processes. On the flip side, a failed software implementation rollout for ERP systems can be massively detrimental to organizations.
Here are 7 of the most infamous ERP failures from the last ten years that cost Fortune 500 companies hundreds of millions of dollars and set them back years, why it happened, and how you can avoid the same fate:
1. Hershey’s Failed ERP Implementation Cost Them Over $100 Million
In the late nineties, Hershey discovered their legacy systems had a high risk of being affected by the Millennium Bug. Instead of spending lots of money to fix the date-related issues, they decided to replace their ERP. They chose to implement three separate ERP solutions from SAP, Siebel, and Manugistics, which proved too complicated and disjointed for the company to use properly, and their self-imposed deadlines proved to be unrealistic.
Hershey would go on to lose more than $100 million in orders for products they had in stock and experienced an 8% drop in their stock price in one day. The company eventually recovered a year later and completed full integration of an SAP ERP in 2002.
Why Hershey failed: Hershey’s mishap is one of the first major examples of an ERP failure at the highest echelons of business. Today, it serves as a landmark case study on a lack of due diligence and a disjointed ERP configuration.
2. Mission Produce's failed ERP transformation
In 2021, Mission Produce launched a new ERP system to manage its purchasing, inventory, and financial operations. The ERP transformation was intended to support its international growth plan with better operational visibility, automated financial reporting, and integration of data sources
At launch, Mission Produce quickly realized its ERP change project had gone sideways. The company lost visibility into core operation metrics, like the number of avocados in its inventory, their level of quality (i.e., whether they were ripe or had gone bad), whether orders had been shipped, whether invoices had been paid, and other foundational Mission Produce business and supply main metrics.
The ERP change failure forced the company to revert to manual processes on the fly to keep up with its distribution and operations and fulfill all customer orders. Eventually, Mission Produce hired a third-party ERP consulting group to help get its ERP transformation back on track, but only after it cost the company nearly $4M in over-budget costs and delayed the ERP launch by 9 months.
Why Mission Produce failed: While Mission Produce’s CEO told investors that they had spent hundreds of hours planning and preparing for the ERP migration and implementation, he admitted that “the extent and magnitude [of the ERP change] was greater than we anticipated.”
Mission Product’s change initiative failed because it was naïve to how foundational its ERP is to its business operations. The company failed to properly prepare for the ERP implementation from multiple perspectives, including a failure to adequately set up and configure, not beta test it in a sandbox environment or with a beta launch, and a lack of ERP end-user training to enable employees to use the ERP correctly.
3. Waste Management Claimed $500 Million in Losses After ERP Failure
A lawsuit filed by Waste Management against SAP in 2008 brought the company to the public’s attention. In the lawsuit, SAP was accused of providing a software mockup that was modified to appear as if it was fully functional.
Initially, Waste Management claimed losses of $100 million from both implementation costs and loss of revenue. They later bumped that number up to $500 million. Both parties would settle out of court two years after the initial lawsuit.
Why Waste Management failed: In the end, their implementation failed because they didn’t dig into the details of the software they chose. This case demonstrates the importance of due diligence when assessing the ability of an ERP provider to deliver on its promises.
4. Revlon’s post-merge ERP consolidation project failure
Revlon, a well-known cosmetics company, acquired competitor Elizabeth Arden in 2016. This presented challenges for Revlon as it merged business units and integrated processes across the two entities – each having its own, custom-built ERP processes and operational workflows.
At the time, both companies had successfully implemented an ERP that worked for them (Elizabeth Arden with Oracle Fusion, Revlon with Microsoft Dynamics AX). Still, they understood they would need to consolidate its ERP systems to avoid future problems, operate efficiently, and sustain future growth. Instead of building on one of the two ERP systems that had worked for its now-integrated business applications team previously, Revlov chose an entirely new ERP system, SAP S4/HANA.
The change failure was so disruptive that it shut down a core Revlon manufacturing facility in North Carolina, resulting in millions of dollars in lost sales. This had a downstream impact, causing the company to incur shipping fees and damaging its customer service reputation. It also resulted in its stockholders suing the company due to the negative impact the failure had on Revlon’s stock price.
In early 2019, Revlon broke the ERP failure news on a shareholder call — their stock fell almost 7% within 24 hours, and the confession triggered multiple lawsuits by investors. Revlon dedicated $54 million toward reversing the damage at their North Carolina facility, which included trashing the S/4HANA system.
Why Revlon failed: Early in its implementation, Revlon realized the ERP consolidation change project was doomed to fail. Revlon leadership cited poor ERP design, process mapping, integration, and IT maintenance as core reasons the implementation failed. This was no doubt heightened by the complex requirements of integrating two entirely separate workflows built on two different systems down into one centralized system. Revlon said a “lack of design and maintenance of effective controls” in connection with the ERP implementation was the reason for the failure. In a nutshell, they misjudged the risks of implementing S/4HANA and didn’t have the right processes to properly manage the project.
5. Lidl Lost 7 Years Due to an ERP Implementation Failure
In 2011, German grocery chain Lidl worked with SAP to develop a modernized inventory management system. The partnership made perfect sense, and the transition was expected to be smooth. Unfortunately for Lidl, their unique method of record-keeping threw a wrench in the works and introduced several issues during their implementation process.
The result was over $580 million dollars and seven years of development down the drain. After all that time and energy spent, Lidl went back to their existing in-house inventory management system.
Why Lidl failed: Lidl’s downfall was in large part due to project-scope mismatches. The grocery chain wouldn’t make the needed adjustments to their existing processes, and without that willingness to change, they failed to sync with SAP’s new technology.
6. The US Navy Wasted 7 Years on ERP Implementation
From 1998 to 2005, the U.S. Navy tried — and failed—to launch a proper ERP system on four separate occasions. A report from the Government Accountability Office stated the small scope and redundancies of the ERP systems did not fulfill Navy requirements.
The cost of the four projects was gigantic — to the tune of $1 billion in total. Ultimately, the Navy worked with SAP again to develop a consolidated system — three of the four ERPs were discontinued and replaced with a single SAP application.
Why the U.S. Navy failed: The Navy’s mistakes showcase that an ERP too small in scope can be just as damaging as one that is too large. To find the right fit, stakeholders need to scale their requirements to align with their true business needs.
7. Nike’s ERP Implementation Disaster Led to $500 Million in Lost Sales
Around the turn of the 21st century, Nike was the premier name in the sneaker industry. To secure their market dominance, the company worked with i2 Technologies to develop an ERP solution for the company’s demand planning processes. However, Nike’s leadership rushed the timeframe, and their new ERP went online with major bugs that tanked the company’s ability to distribute their flagship product at the time — Air Jordans.
The result was a total loss of $500 million dollars from both lost sales and project costs, as well as several lawsuits resulting from unfulfilled orders. They adopted a more robust SAP ERP in 2003.
Why Nike failed: Nike’s unrealistic timeframe caused their implementation to spiral out of control and led to a serious hit to their revenue.
8. HP’s ERP Migration Caused $160 Million in Lost Sales
Computer hardware giant HP sought to migrate one of their largest divisions onto an ERP system from SAP in 2004. The company’s IT division already had success migrating five of HP’s other manufacturing arms onto SAP systems, with contingency plans in place to help with the transition. Unfortunately, the contingency plans weren’t enough to save them —their supply chain was unable to keep up with the backlog of orders resulting from bugs in the new system.
The $30 million migration ended up costing HP $160 million in lost sales — a $120 million order pileup that led to $40 million in revenue losses. They eventually cut their losses and sorted out their supply chain and ERP issues the following year.
Why HP failed: HP’s blunder illustrates the importance of change management. Their CIO blamed their implementation team, citing issues such as not collaborating across silos and ineffective practices with manual inputs.
What Are Common Reasons for ERP Implementation Failure?
Many ERP failures are caused by unexpected technical or organizational issues. Some companies don’t effectively research their ERP software to determine if it meets their business requirements. Others are overly optimistic about implementation timelines.
ERPs can be complex, and implementation requires multiple components and interdependencies, which increases the vulnerability to project failure. Underestimating the complexity and the effort required to install, configure, and roll out a new system is a recipe for failure.
By avoiding some of the most common issues with ERP implementation, you can reduce your chances of failure and keep costs minimal.
1. Poor Change Management
Improperly defining business processes and not paying enough attention to change management can lead to implementation failures. For ERPs to succeed, employees have to adapt to new processes and adjust to new technology. This is a challenging task for any size organization and even more difficult for organizations at the enterprise level.
2. Lack of Onboarding & Traiing
Lack of proper ERP onboarding and training results in a greater likelihood of poor digital adoption and ERP failure. Any transition to new technology should be accompanied by proper preparation, instruction, and a full implementation plan — no one can benefit from a new system if they don’t know how to use it.
3. Project Scope
Project scopes that are mismatched with organizational needs can cause ERPs to go over budget and miss deadlines. For example, the scope may be too large for the chosen timeframe, or the project could fall victim to scope creep. Both issues can cause missed deadlines and budget overruns.
4. Unrealistic Expectations
Overestimating an ERP’s abilities is a recipe for failure. Implementing a new ERP can reduce costs and increase productivity, but expecting it to solve all of the company’s problems will lead to trouble.
5. Lack of Due Diligence
Many organizations jump right into a new implementation project without spending enough time on the basics. A new system is needed, a vendor is found, and a contract has been signed. But don’t forget the basic questions. Will this integrate with my existing systems? How will I support my IT team post-launch? How will end-users be able to get support on questions?
ERP Systems Click Better With Whatfix
ERP implementation and transformation projects are often complex, expensive, and potentially risky. However, many organizations are presented with even higher risks if they fail to update their ERP systems and keep up with modern solutions.
For many organizations, ERP systems are mission critical, with their core operations not being able to function without it.
Whatfix empowers organizations to realize the value of their ERP investments, accelerate transformation projects, maximize ERP ROI, and achieve business outcomes.
Whatfix offers three no-code products that drive ERP adoption, accelerate ERP implementations, and enable enterprises to successfully consolidate ERP systems with minimal user downtime and fast time-to-proficiency.
- Whatfix DAP to enable ERP end-users with contextual in-app guidance and on-demand help that supports employees in the flow of work.
- Whatfix Mirror to quickly create ERP sandbox environments for hands-on simulated training and user testing.
- Whatfix Product Analytics to empower ERP application owners and department leaders to capture ERP end-user behavior, product usage, and process completion rates.
With Whatfix, organizations can overcome the challenges of ERP consolidation and transformation projects by focusing on the end-user experience, including:
1. Easily create ERP sandbox environments for hands-on user training
With Whatfix Mirror, IT teams can quickly create ERP sandbox environments for hands-on training. This enables organizations to conduct user testing before launch to identify friction areas and ensure processes work smoothly.
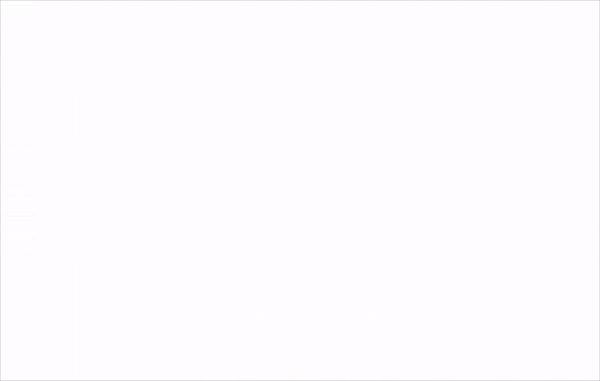
More importantly, it provides a simulated ERP user onboarding experience during migration and for newly onboarded employees who provide hands-on training without impacting real ERP data or processes. Employees can interact with ERP processes, navigate through the modules and tasks they’re responsible for, and run through guided experiences and scenarios – all without the fear of impacting actual operations or your ERP’s data quality.
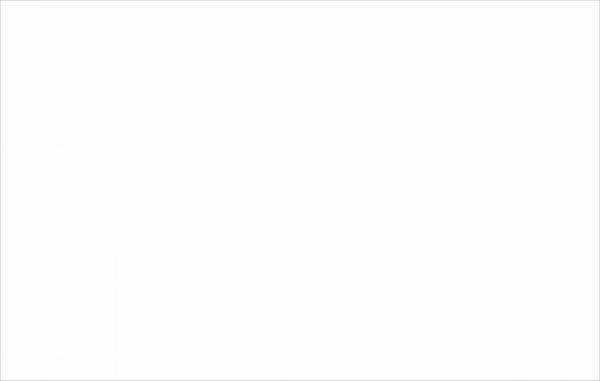
2. Create role-based ERP end-user guidance
ERPs are used by countless teams and departments, with use cases ranging from accounts payable, procurement, audits, billing, vendor management, customer relations – the list goes on. ERPs are also highly customized to meet the specific needs of organizations and departments.
With Whatfix, create role-based ERP in-app guidance that provides contextual information and support to your various end-users in the flow of work.
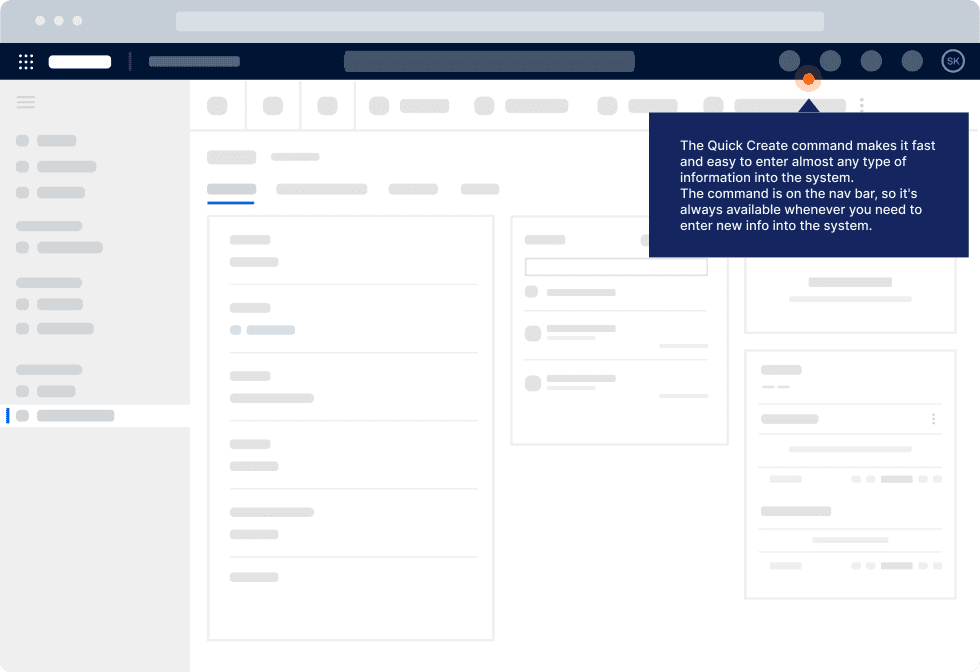
With Whatfix, create role-specific in-app experiences contextual to where users are in an ERP, like:
- In-app Flows to walk end-users step-by-step through complex ERP tasks.
- Task Lists to onboard new ERP end-users and guide them through their first steps and core workflows.
- Pop-Ups to drive awareness of ERP process changes, make team announcements, alert users to upcoming deadlines or new compliance laws, announce new training resources, and more.
- Smart Tips to provide additional context or nudge different users to take specific actions.
- Field Validation to ensure that your ERP end-users enter data in the correct format.
IT teams and ERP application owners can take a continuous improvement approach to its in-app guided tutorials with Guidance Analytics. Understand how users engage and consume your in-app content to answer questions like, “How many new employees are completing their new user task list?”, “How often do employees click on in-app Smart Tips”, and “What ERP support issues are employees searching for the most?”.
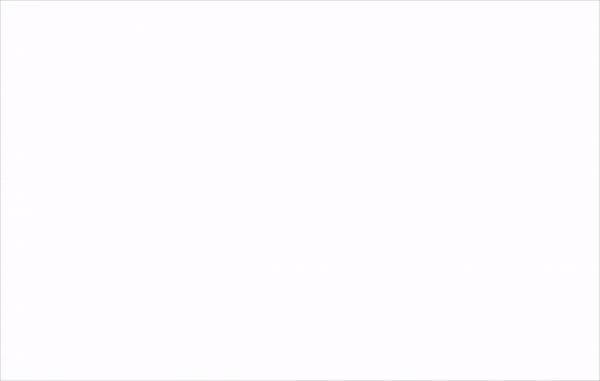
3. Provide real-time user support in the flow of work
With Whatfix, go beyond ERP user onboarding and one-time training with Self Help. Self Help provides an on-demand, in-app help center that overlays your ERP UI. ERP users can use its search function to find any help or support resource they need, at the moment of need, without leaving the application. Self Help also presents contextual support and information depending on where a user is at in your ERP.
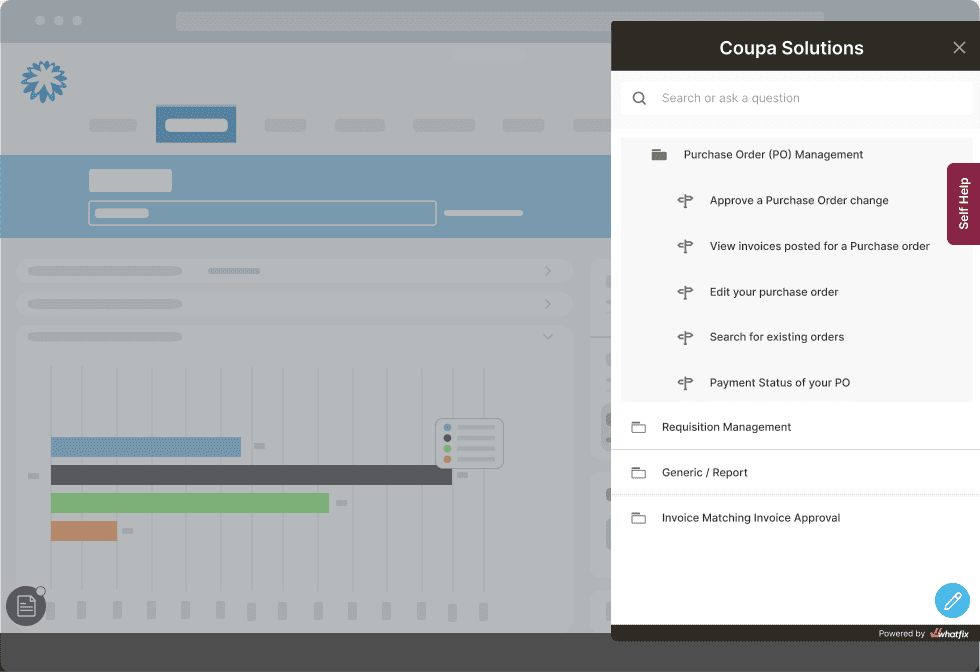
Self Help integrates with your ERP training resources, IT Help Desk, SOPs, LMS, vendor support content, third-party links, and more – aggregating it into a searchable self-help wiki. Attach Self Help entries to in-app guided Flows that are prompted when an end-user interacts with the widget. Analyze what your end-users are searching for and are experiencing friction with to identify areas of ERP improvement and new support resources to create.
Renewables energy enterprise REG partnered with Whatfix to support its JD Edwards ERP transformation project. With Whatfix’s in-app guidance, user support, and process analytics, REG reduced its ERP time-to-proficiency for new users by 50%, equal to a 3-month reduction in getting new employees up to speed with its highly customized JD Edwards ERP instance. Self Help enabled its ERP users with on-demand support, deflecting ERP-related support tickets which resulted in a 600% reduction in application-related support cases and tickets.
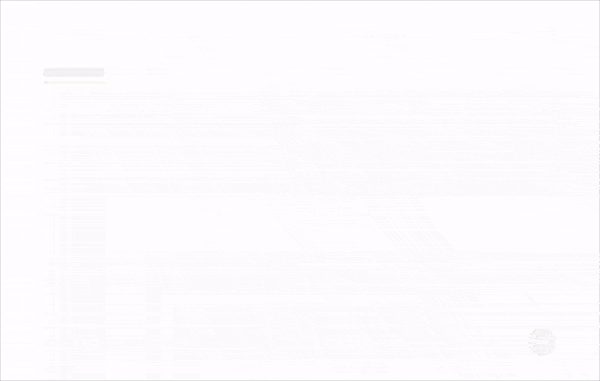
4. Localize ERP in-app guidance and support
Many ERP consolidation projects will need to provide support for their ERP users who are distributed across the global. This presents challenges such as language localization, compliance and regulation requirements, and other regional issues.
With Whatfix, automatically localize your ERP in-app guidance and support content to your end-users, providing personalized support to each end-user. Whatfix supports over 80 languages, providing global content localization and auto-translation features that enable your global ERP end-users, no matter their native or preferred language.
5. Take a data-driven approach to ERP process optimization and UX improvement
Post-ERP implementation, IT teams are faced with challenges of tracking workflow efficiency, testing ERP improvements, optimizing ERP processes, governing ERP processes, and improving user adoption.
Whatfix provides two solutions to enable IT teams with the data and insights they need to make ERP improvements and drive ROI.
Guidance Analytics provides insights into how your ERP users consume and engage with you in-app Whatfix content. Track how many users completed their new user Task List, how many user engaged with a Smart Tip, how many users clicked on the CTA in an announcement Pop-Up, or what are the most searched queries in Self Help.
Whatfix Product Analytics provides ERP application owners with a full no-code event tracking solution to track any custom user action or event. User Funnels and Journeys allow application leaders to identify areas of friction, processes with low completion rates, and where dropoffs occur. Compare segments of users (like departments or regional offices) against one another with Cohorts to identify if adoption or governance issues stem from specific locations or groups of users.
Ready to accelerate your ERP implementation initiative and maximize your transformation investment? Request a Whatfix demo!